Defense Industry
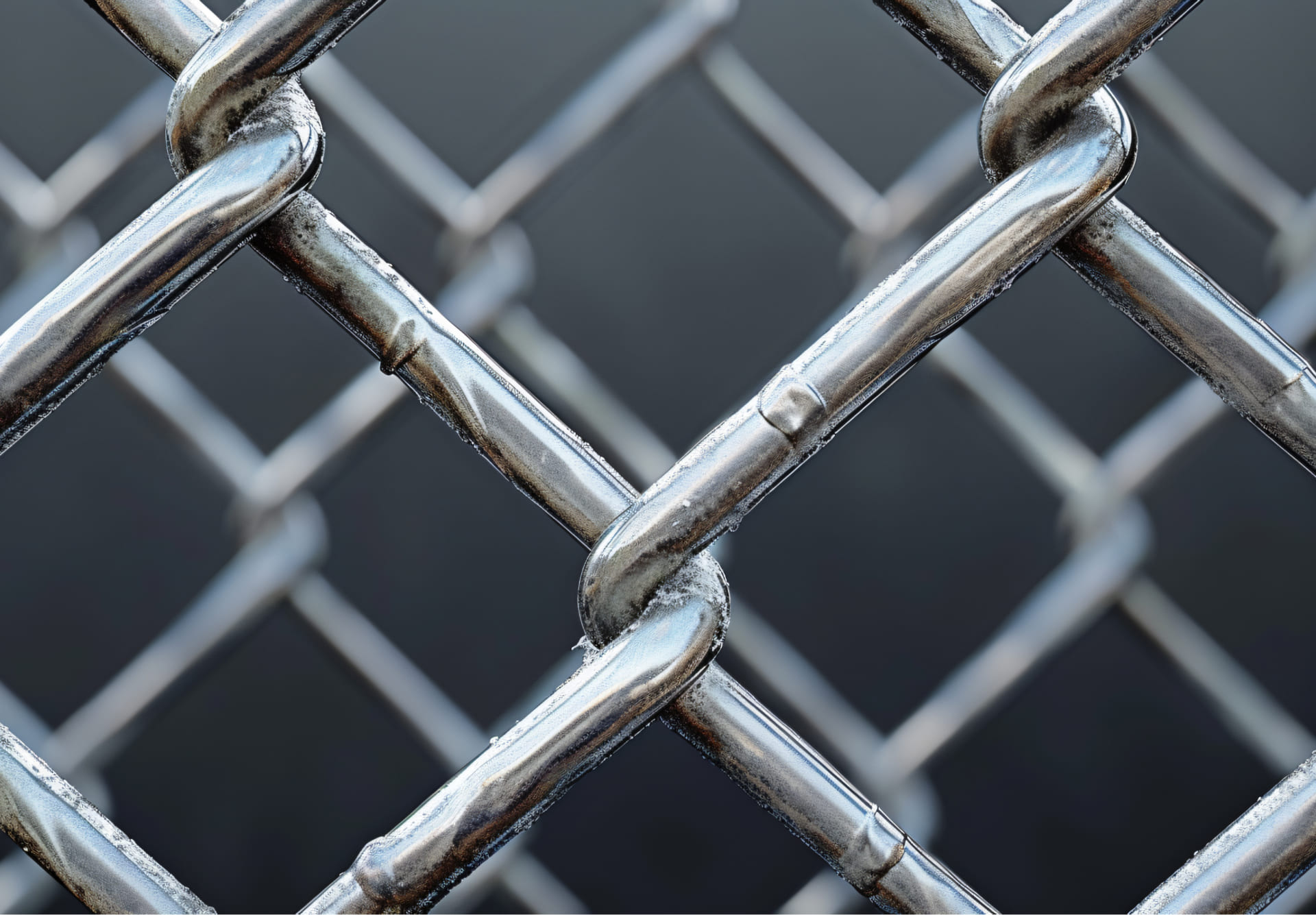
In the defense industry, quality and reliability are critical. TIG Brush provides advanced weld cleaning and surface treatment solutions designed for stainless steel applications in defense projects. Whether it’s equipment, vehicles, or infrastructure, every component must meet strict standards for durability and performance. TIG Brush ensures clean, passivated welds that improves the integrity of stainless steel, making them resistant to corrosion and suitable for the toughest environments.
Defense applications often involve challenging conditions where materials are exposed to extreme wear, high temperatures, and corrosive elements. TIG Brush’s Dynamic Power Transfer technology removes heat tint, surface contamination, and oxidation from stainless steel with precision, ensuring welds are flawless, strong, and long-lasting. From military vehicles to stainless steel infrastructure, TIG Brush helps defense manufacturers maintain the highest quality standards.
Benefits of TIG Brush in the Defense Industry
01. Reliability and Strength
In defense, every detail matters. TIG Brush ensures that stainless steel welds meet stringent defense industry requirements for strength and reliability, providing a dependable solution for mission-critical components. This reduces the risk of corrosion and structural failure, helping to extend the lifespan of equipment in harsh environments.
02. Safety and Compliance
TIG Brush’s cleaning fluids and electric-powered system are safe for workers and meet environmental safety standards, offering a compliant and eco-friendly solution for defense manufacturers. This ensures the defense sector can maintain high safety standards without compromising on weld quality or worker well-being.
03. Corrosion Resistance
Defense equipment and infrastructure are often exposed to extreme environmental conditions. TIG Brush’s ability to passivate welds increases corrosion resistance, ensuring that stainless steel components can withstand prolonged exposure to saltwater, humidity, and other harsh conditions without degradation.